How to Choose Egg Incubator Suitable for Your Breeding Scale
In modern poultry farming, fully automatic incubators have become an indispensable tool, playing a crucial role in both small-scale family farms and large commercial operations. Traditional natural incubation methods are not only time-consuming and labor-intensive but also have inconsistent hatch rates. This is especially problematic in larger farms where such methods cannot meet the high demand. Commercial egg incubators, on the other hand, optimize the incubation environment by precisely controlling temperature, humidity, and ventilation, significantly improving both efficiency and success rates.
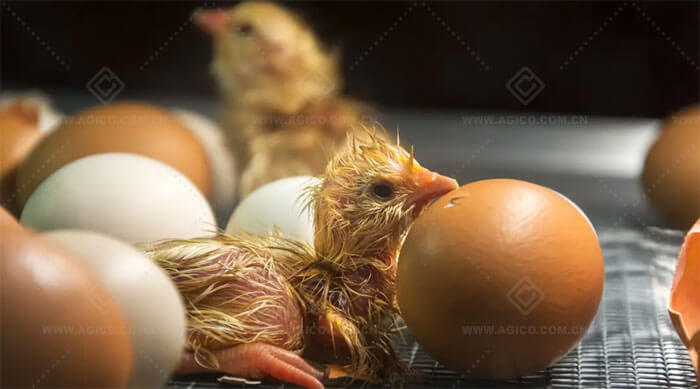
However, choosing the right incubator is vital for farms of different sizes. For small-scale family farmers, a large egg incubator could lead to unnecessary expenses and wasted resources. Conversely, for large commercial poultry farms, opting for a small egg incubator would limit capacity and fail to meet the demands of mass hatching. Therefore, understanding how to select a fully automatic incubator based on the specific scale of your farm is essential. This not only enhances hatch rates but also optimizes resource allocation, ultimately improving overall farming profitability.
Poultry Incubation for Small-Scale Farming
Suitable scenarios
Small-scale family farms typically operate on a smaller scale with relatively low hatching volumes. Farmers in this category often prioritize cost control and ease of operation. They might be raising poultry out of interest, as a hobby, or to supply fresh eggs and meat for their own households. These farmers require an incubator that is both economical and practical to meet their day-to-day hatching needs. Given the limited scale of their operations, they don’t need to handle large volumes of eggs, so the incubator’s capacity and features should align with small-scale use—efficient enough to get the job done without wasting resources.
Recommended incubator models and capacities for small-scale farming
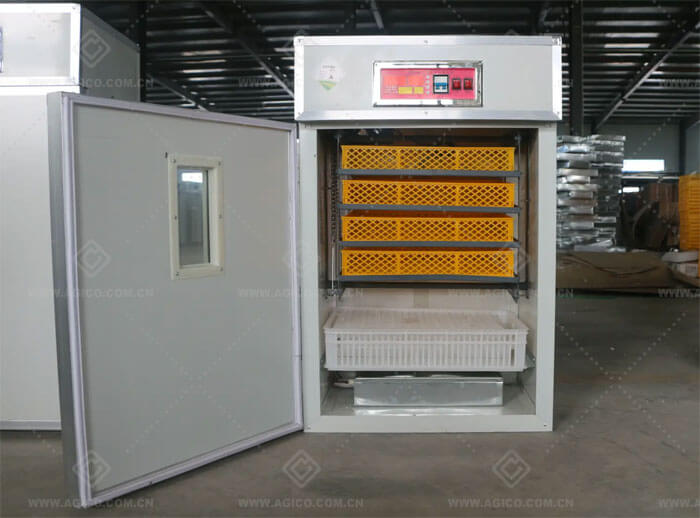
For small-scale family farming, a small egg incubator with a capacity of 88 to 1,000 eggs is recommended. This size of incubator can comfortably meet the needs of small-scale hatching while not taking up too much space, making it ideal for home environments. These small egg incubators are usually compact in design, easy to operate and maintain, and particularly suited for households where space is limited but hatching needs must still be met. For family farmers, a small egg incubator can easily handle daily hatching tasks, whether it’s incubating a few eggs or raising a small number of chicks.
Small egg incubator for sale
Small scale poultry egg incubator capacity(Pcs per set) | Electric heating power(W) | ||||
---|---|---|---|---|---|
Chicken egg | Duck egg | Goose egg | Pigeon egg | Quail egg | |
88 | 63 | 32 | 112 | 221 | 700 |
176 | 128 | 64 | 224 | 442 | 700 |
264 | 189 | 96 | 336 | 663 | 700 |
352 | 252 | 128 | 448 | 884 | 700 |
440 | 315 | 160 | 560 | 1105 | 700 |
528 | 378 | 192 | 672 | 1326 | 700 |
880 | 630 | 320 | 1120 | 2210 | 1000 |
1056 | 756 | 384 | 1344 | 2652 | 1000 |
1232 | 882 | 448 | 1568 | 3094 | 1000 |
1408 | 1008 | 512 | 1792 | 3536 | 1000 |
1584 | 1134 | 576 | 2016 | 3978 | 1000 |
1848 | 1323 | 672 | 2352 | 4641 | 1000 |
Core function requirements
While small egg incubators don’t require the complex and diverse features of larger models, certain core functions remain essential. An automatic temperature control function is a must-have, ensuring that the incubator’s internal temperature stays within the optimal range at all times, thus minimizing the risk of human error. Humidity regulation is equally important, as stable humidity levels during the incubation process can significantly improve hatch rates. Additionally, small incubators should be equipped with a visual hatch window, allowing farmers to monitor the incubation progress without needing to frequently open the incubator, which could disrupt the internal environment. These core features make it easy for home users to manage the entire incubation process, even if they are beginners with no prior experience.
Poultry Incubation for Medium-Scale Farming
Suitable scenarios
Medium-scale farms operate on a larger scale than small family farms but haven’t yet reached the level of large commercial operations. Their characteristics differ from both smaller family farms and large poultry farms. These farms typically handle a moderate number of eggs, ranging from several hundred to a few thousand, to maximize hatching efficiency and output within limited space and resources. Medium-scale farms have high demands for cost-effectiveness, needing to maintain a high hatching success rate while controlling operational costs. Therefore, the selection of an incubator must strike a balance between capacity, functionality, and economic viability to support ongoing, efficient production.
Recommended incubator models and capacities for medium-scale farming
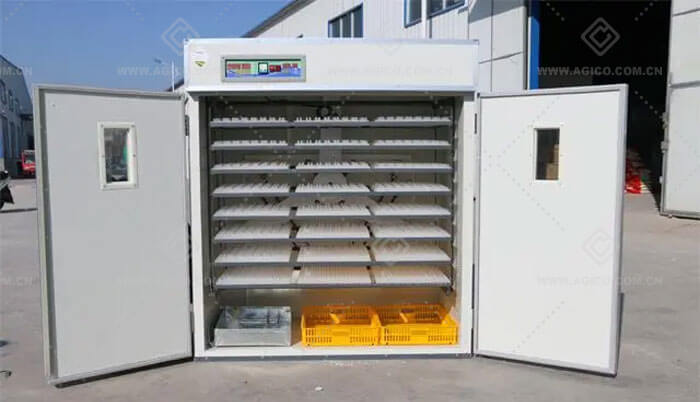
For medium-scale farms, incubators with a capacity of 2,000 to 8,000 eggs are ideal. This size of incubator can meet the hatching needs of medium-sized operations without compromising efficiency. These incubators often feature modular designs, allowing for flexible capacity adjustments to suit different hatching schedules. Additionally, they are relatively simple to operate, making them suitable for everyday use on the farm. They can handle occasional peak demands while maintaining steady output during regular operations. Choosing an appropriately sized incubator can help medium-scale farms avoid excessive initial investments while ensuring they can meet potential future expansion needs.
Medium-scale egg incubator for sale
Medium scale poultry egg incubator capacity(Pcs per set) | Electric heating power(W) | ||||
---|---|---|---|---|---|
Chicken egg | Duck egg | Goose egg | Pigeon egg | Quail egg | |
2112 | 1512 | 768 | 2688 | 5304 | 1600 |
2376 | 1701 | 864 | 3024 | 5967 | 1600 |
2640 | 1890 | 960 | 3360 | 6630 | 1600 |
2816 | 2016 | 1024 | 3584 | 7072 | 1600 |
3168 | 2258 | 1152 | 4032 | 7956 | 1600 |
3520 | 2520 | 1280 | 4480 | 8840 | 1600 |
3872 | 2772 | 1408 | 4928 | 9724 | 2000 |
4224 | 3024 | 1536 | 5376 | 10608 | 2000 |
4576 | 3276 | 1664 | 5824 | 11492 | 2000 |
5280 | 3780 | 1920 | 6720 | 13260 | 2000 |
6336 | 4536 | 2304 | 8064 | 15912 | 2000 |
8448 | 6048 | 3072 | 10752 | 21216 | 3200 |
Technical function requirements
To achieve high success rates in medium-scale hatching, incubators must be equipped with several essential technical features. A temperature equalization system is crucial for ensuring that every egg incubates under uniform conditions. This system automatically adjusts and evenly distributes the temperature inside the incubator, preventing hatching failures caused by temperature differences. Humidity control is equally important; it automatically regulates the humidity levels within the incubator, ensuring proper embryo development throughout the hatching process. An automatic egg-turning function is also indispensable, as it simulates the natural process of a hen turning its eggs, preventing the embryos from sticking to the shell and thus improving hatch rates. These technical features work together to ensure that medium-sized incubators can maintain high production efficiency while delivering consistent hatching quality.
Poultry Incubation for Large-Scale Commercial Farming
Suitable scenarios
The operational characteristics of large commercial poultry farms differ significantly from those of small and medium-scale farms. The primary goal of large farms is mass production to meet high market demand. Such farms typically handle tens of thousands of eggs, requiring more advanced incubation equipment. They need high-capacity incubators to support large-scale production, along with highly automated management systems to reduce the frequency and cost of manual intervention. With increasing market competition and rising labor costs, minimizing operational expenses, boosting production efficiency, and ensuring high hatching success rates are the key considerations for large commercial farms when selecting equipment.
Recommended incubator models and capacities for large-scale farming
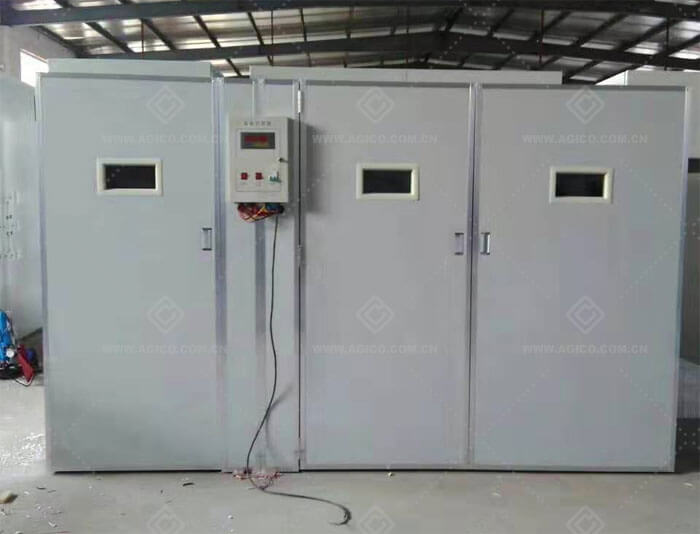
For large commercial poultry farms, incubators with a capacity of 9,000 to 20,000 eggs are recommended. These high-capacity large egg incubators can handle a large number of eggs in a single hatching cycle, significantly increasing production efficiency and ensuring that the farm can consistently meet market demands. Choosing the right capacity incubator not only supports efficient production but also reduces the intervals between batches, maximizing equipment utilization. Additionally, large egg incubators are typically designed to be robust and capable of withstanding long-term, high-load operations, making them well-suited for the continuous demands of large farms. The efficiency of high-capacity equipment makes it an essential tool for large commercial farms, helping them maintain competitiveness in large-scale production.
Large incubator for eggs
Large scale poultry egg incubator capacity(Pcs per set) | Electric heating power(W) | ||||
---|---|---|---|---|---|
Chicken egg | Duck egg | Goose egg | Pigeon egg | Quail egg | |
9856 | 7056 | 3584 | 12544 | 24752 | 3200 |
12672 | 9072 | 4608 | 16128 | 31824 | 4800 |
14784 | 10548 | 5376 | 18816 | 37128 | 4800 |
16896 | 12095 | 6144 | 21504 | 42432 | 6400 |
19712 | 14112 | 7186 | 25088 | 49504 | 6400 |
22528 | 16128 | 8192 | 28672 | 56576 | 6400 |
Advanced features and technical requirements
Large commercial poultry farms demand highly advanced technology in their incubators, as cutting-edge incubation technology is crucial for achieving large-scale production and efficient management. An automatic data monitoring feature is essential for real-time tracking of critical parameters such as temperature, humidity, and oxygen levels during the incubation process. This feature automatically adjusts these parameters to their optimal levels, ensuring that each batch of eggs is incubated under the best possible conditions. The intelligent control system can automatically adjust various incubation parameters according to the preset incubation cycle, reducing the need for manual intervention while increasing hatching success rates. The remote management function allows farm managers to monitor and control the incubator’s operational status from anywhere, using a computer or mobile device, and quickly respond to any anomalies. The combination of these technological features makes large egg incubators not only easy to operate but also significantly reduces labor costs, enhancing the reliability and stability of the hatching process.
Incubator Comparison and Selection Guide for Different Scales
Matching incubator capacity with farm size
When selecting a poultry incubator, capacity is a critical factor that directly affects the suitability and efficiency of the equipment. The capacity of the poultry incubator should be matched to the size of the farm to ensure that the equipment neither wastes resources nor limits production. As an experienced incubator supplier, AGICO offers a range of incubators in different sizes and capacities to meet the needs of various farming operations.
Incubator Capacity | Suitable Farm Size | Key Advantages | Key Disadvantages |
---|---|---|---|
88-200 eggs | Small-scale farms | Affordable, easy to operate, space-saving | Limited capacity, not suitable for large-scale hatching |
500-2000 eggs | Medium-scale farms | Balanced capacity and efficiency, multifunctional support, adaptable | Higher price, significant initial investment cost |
5000-20000 eggs | Large commercial farms | High capacity, high automation, remote management | Complex equipment, high initial investment and maintenance costs |
Balancing price and performance in incubators
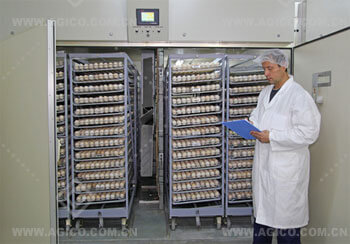
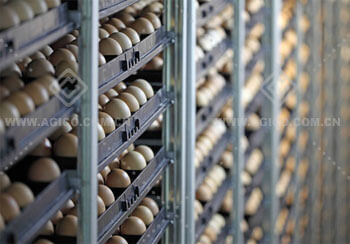
When selecting an incubator, balancing price and performance is a key concern for many poultry farmers. While higher-priced incubators often come with more advanced features and larger capacities, cost-effectiveness can be the deciding factor for some farmers. For small-scale family farmers, an incubator with a moderate price can meet basic needs, making high-end equipment unnecessary. Medium-scale farms need to find a balance between performance and cost, opting for equipment that enhances hatching efficiency and reduces labor costs. Although the initial investment might be higher, increased production and success rates can lead to cost recovery and profitability in the medium term. For large commercial poultry farms, priority should be given to the performance and automation of the equipment. Despite the higher price, the improvements in efficiency and long-term cost savings provided by such equipment can significantly enhance overall profitability.