Briquetting Plant
Developing Trend Of Briquetting Plant
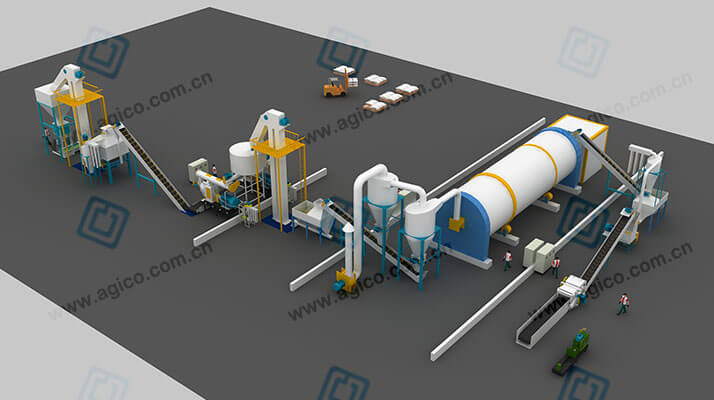
Due to the increase on the cost of conventional fuel(such as coal and gas) and the need for new energy source, more people start to focus on "green" fuel business to use briquetting plant produce renewable, clean and eco-friendly fuel briquettes. We are committed to designing complete biomass briquette plant for customers. Our briquetting plant is suitable for customers from agro-forestry countries with a desire to convert biomass waste into valuable biofuel for domestic use or for exportation, and also our biomass pellet mill and briquetting machines are best choice for individual user who has focused on biofuel production under government support.
About different requirements for biomass briquette plant from customer, our experts will be able to configure a range of equipment for the briquetting plant, including crusher, automatic proportion feeder, double paddle mixer, dryer, biomass briquetting press, conveyor, distribution cabinet, etc. According to processing of fuel briquetting plant raw materials for the choice of stamping briquetting press machine series or screw briquetting machine series equipment to help the user to carry on the processing operation.
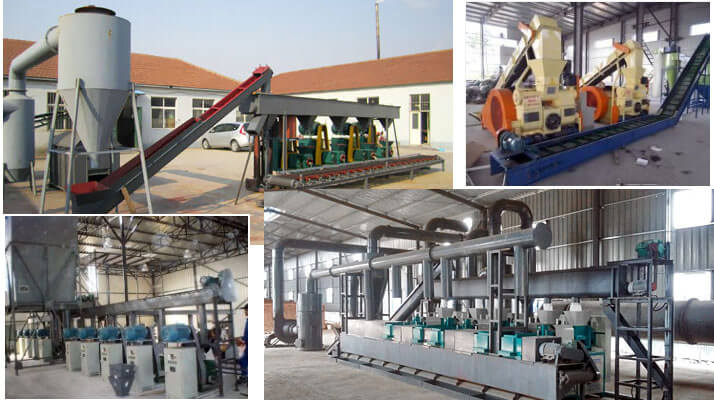
Different needs, different raw materials, corresponding to different equipment needs. We will according to the information provided by the user to design a suitable briquetting plant, in the days after the production process to give the user the highest income benefit!
Fuel Briquetting Plant Process
Raw Material—>Crushing—>Feeding—>Mixing—>Pressing—>Drying—>Briquettes
The raw materials which need to be processed are feed to the briquetting machine through the feeding machine, and the finished products are discharged from the discharge port. Part of the raw material processing of finished product requires the dryer for drying. The whole process is based on the types of raw materials processed by our technical staff for the selection the related equipment for our customers!
The technical innovation of fuel briquetting plant is as follows:
- The use of raw materials, cross cutting, longitudinal method of rubbing the raw materials before processing, make the raw edges more soft and fluffy, not only can reduce the compression resistance, reduce wear die and roller, improve production efficiency, but also in the raw material with high water content period of the implementation of fast drying, shorten the drying time, can save raw materials nutrition maximum limit, improve the utilization rate of biomass briquette plant equipment.
- Using multi-stage progressive spiral feeder, can increase the feeding amount of ring die, reduce pressing resistance, improve the quality of products.
- The forming machine in the briquetting plant adopts the split type assembling ring structure, the inner and outer ring modes are made in a separate way, the process is simplified, the processing is convenient, the cost is reduced, the repair is convenient, the abrasion resistance is good, and the impact resistance is strong.
- The fuel briquetting plant is an eccentric extruded structure with a press roll. Pressure roller, strong screw feeder synchronous rotation and autobiography, so that all the raw materials can be fully pressed into the ring mold. The pressure roller is made of carbon structural steel material, after forging processing, hardfacing alloy, so that the pressure roller surface hardness, wear resistance, impact toughness, easy to repair, can extend the service life of the root.
- The use of motor, gearbox direct transmission, transmission torque, unit linear layout, simple structure, petite size, easy to move, easy to use.
- Voltage cut and compacted together, just need once molding, reduce the repeated environment, just one person can complete all the operation of the briquetting plant.